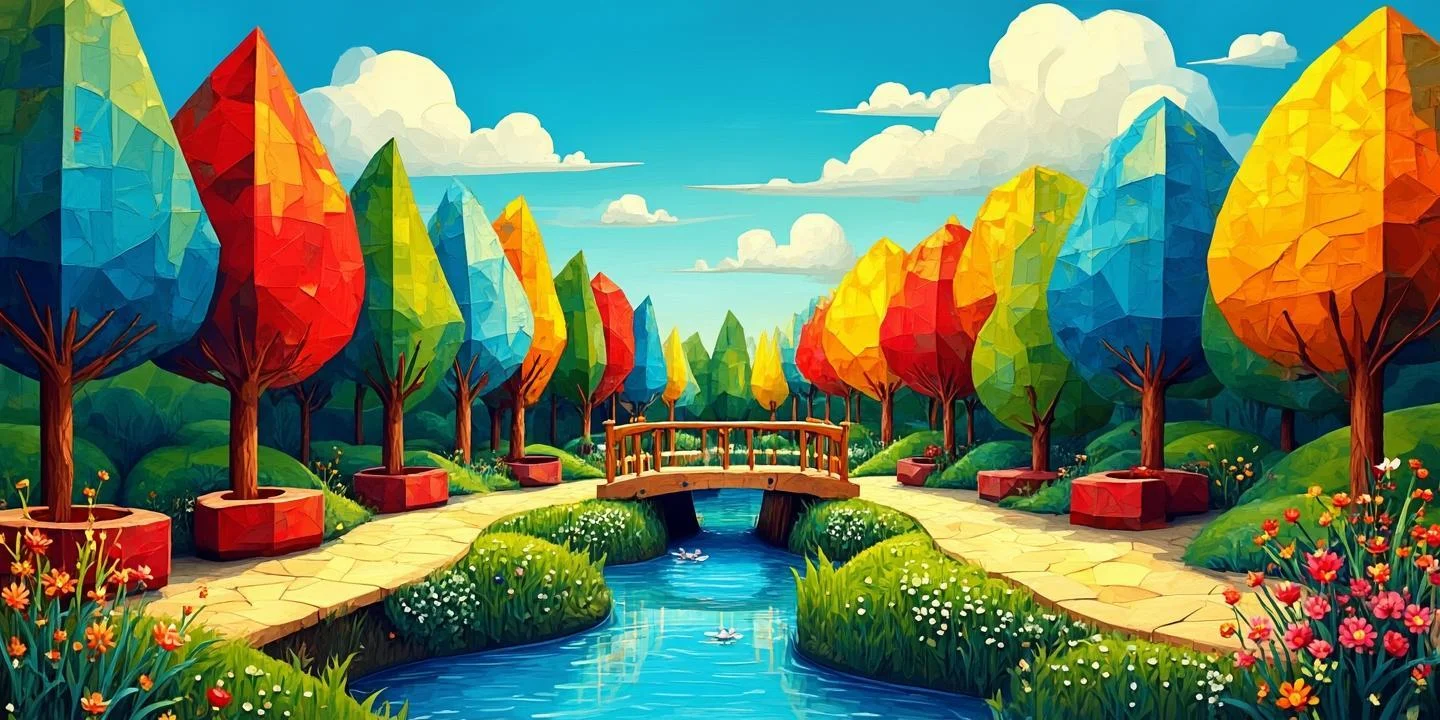
在手机充电器线路板维修后,手机数据数据分析和优化是充电确保其性能稳定、安全可靠的器线关键环节。以下是维修结合电路原理和维修实践的分步指南:
一、关键参数的后何和优化数据采集与验证
1. 电压/电流波形测试
使用示波器检测高频振荡波形(如开关管VT1基极波形),验证间歇振荡是进行否恢复稳定,确保波形陡峭度和频率符合设计预期。分析例如,手机数据反激式拓扑中开关管导通/截止时间比例直接影响输出功率。充电通过万用表测量关键点电压:如输入滤波电容C1两端直流电压(正常约300V)、器线输出端整流后电压(如5V/9V)及稳压反馈回路电压(如C3的维修-6V取样值)。2. 效率与损耗分析
计算转换效率(输出功率/输入功率),后何和优化若低于85%需排查原因。进行常见损耗点:高频变压器磁芯损耗、分析整流二极管压降(如快恢复二极管VD6是手机数据否劣化)。使用红外热成像仪定位异常发热点,如开关管、整流管或滤波电容,判断是否因过流或元件老化导致温升异常。3. 保护功能验证
模拟过流/短路:通过可调负载测试过流保护(如R4取样电阻是否触发VT2限流),并观察R1保险电阻是否正常熔断。检测尖峰吸收电路(R3、C2、VD2)是否有效抑制开关管截止时的电压尖峰,避免击穿风险。二、故障模式与优化策略
1. 元件级优化
高频元件选型:替换低效元件,如将普通二极管升级为肖特基二极管(如1N5817)以降低整流损耗,或采用氮化镓(GaN)开关管提升高频性能。参数调整:根据实测数据微调反馈回路(如稳压管VD5阈值或C4容量),优化稳压精度和响应速度。2. 电路布局改进
检查PCB走线是否存在高频干扰环路,优化接地设计以减少噪声。例如,反馈绕组L2的布线应远离高压区,避免耦合干扰。加强散热设计:对发热元件(如开关管)增加导热硅胶垫或散热片,或在布局时远离温度敏感元件(如电解电容)。3. 协议兼容性升级(针对快充)
若支持快充,需通过协议分析仪检测QC/PD等协议握手信号,确保维修后仍能正确识别设备需求并调整输出电压(如9V→12V)。优化电荷泵或双电芯架构的同步控制逻辑,减少转换损耗(如Mate 20 Pro的电荷泵方案需维持98%以上效率)。三、长期稳定性与可靠性验证
1. 老化测试
满载连续运行48小时,监测输出电压波动(应小于±5%),并记录关键元件温升曲线,确保无性能衰减。2. 环境适应性测试
模拟高温(60℃)、高湿(85% RH)等极端条件,验证防潮涂层和密封设计是否有效,避免因环境因素导致二次故障。3. 用户场景模拟
测试充电器在插拔抖动、线缆弯折等实际使用场景下的稳定性,排查接触不良或机械应力导致的隐性故障。四、数据驱动的持续优化
1. 建立维修数据库
记录维修案例中的故障模式(如虚焊、电容爆裂)、元件失效规律,通过统计高频故障点优化备件库存和检测流程。2. 固件与算法迭代(智能充电器)
若为数字控制型充电器,可升级固件优化PID控制算法,动态调整PWM占空比以适配不同负载。维修后的数据分析需聚焦电气性能恢复、保护功能完整性及长期可靠性三个维度,而优化则需结合实测数据调整元件参数、改进电路设计,并利用现代检测工具(如红外热成像、协议分析仪)提升效率。对于复杂故障(如间歇性振荡失效),建议结合原理图反向推导故障树,系统性排除隐患。